- My Forums
- Tiger Rant
- LSU Recruiting
- SEC Rant
- Saints Talk
- Pelicans Talk
- More Sports Board
- Fantasy Sports
- Golf Board
- Soccer Board
- O-T Lounge
- Tech Board
- Home/Garden Board
- Outdoor Board
- Health/Fitness Board
- Movie/TV Board
- Book Board
- Music Board
- Political Talk
- Money Talk
- Fark Board
- Gaming Board
- Travel Board
- Food/Drink Board
- Ticket Exchange
- TD Help Board
Customize My Forums- View All Forums
- Show Left Links
- Topic Sort Options
- Trending Topics
- Recent Topics
- Active Topics
Started By
Message
Pole Barn/Post Frame vs Red Metal Workshop (24x42 with lean to)
Posted on 9/20/24 at 8:53 am
Posted on 9/20/24 at 8:53 am
Good morning!
Wanted to seek out some of y'alls opinions on a workshop I'm trying to build. This one will be pretty close to my house, so appearance is important to me and quality is going to be critical. We wanted this to be pretty low key, fairly low slung, and serve as both a workshop for me and eventually have an air conditioned space in the back for a hobby shop for my wife.
One theme I've been hearing is to build bigger than I anticipate I will need, which is what I'm going to try to do.
I'm looking at a higher end Mallet building (pole barn) and a Mueller building, but I'm open to alternatives. Trying to make them as close to apples to apples as I can. I don't like that I can't seem to do overhangs with the Mallet products, and I also don't like the exposed red iron in the lean to for the Mueller building. Wish there was an option to remedy both of those issues.
Some questions
How long do pole barns tend to last? I've seen some that are easily 80-90 years old but are pretty bent up but still standing. Is that a possibility with these newer ones? Are we as good with wood treatment as we used to be?
What should I be looking for during the design and construction process?
How much head space do I need above a roll top door to accommodate the rolling mechanism?
If you've built one recently - any lessons learned that you'd be willing to share?
The Mallett buildings I've seen have that fiber/fuzzy looking concrete pad poured inside. I know that prevents surface cracks, but is it possible to put a rolled on epoxy finish on that?
With the insulated panels, how much heat should I expect in there? How much A/C would I need to keep it reasonable in an approximately 1,000 square foot space?
This is sort of what I'm looking at building. The lean to would be sort of a porch for us facing the rest of our property. This building will be as far to the back corner as I'm legally allowed to build. Planning on a 10' head height with an 8' wide lean to. Trying to get a 4/12 roof pitch.
We will be roughing in plumbing; and electrical will be going in as well.
Wanted to seek out some of y'alls opinions on a workshop I'm trying to build. This one will be pretty close to my house, so appearance is important to me and quality is going to be critical. We wanted this to be pretty low key, fairly low slung, and serve as both a workshop for me and eventually have an air conditioned space in the back for a hobby shop for my wife.
One theme I've been hearing is to build bigger than I anticipate I will need, which is what I'm going to try to do.
I'm looking at a higher end Mallet building (pole barn) and a Mueller building, but I'm open to alternatives. Trying to make them as close to apples to apples as I can. I don't like that I can't seem to do overhangs with the Mallet products, and I also don't like the exposed red iron in the lean to for the Mueller building. Wish there was an option to remedy both of those issues.
Some questions
How long do pole barns tend to last? I've seen some that are easily 80-90 years old but are pretty bent up but still standing. Is that a possibility with these newer ones? Are we as good with wood treatment as we used to be?
What should I be looking for during the design and construction process?
How much head space do I need above a roll top door to accommodate the rolling mechanism?
If you've built one recently - any lessons learned that you'd be willing to share?
The Mallett buildings I've seen have that fiber/fuzzy looking concrete pad poured inside. I know that prevents surface cracks, but is it possible to put a rolled on epoxy finish on that?
With the insulated panels, how much heat should I expect in there? How much A/C would I need to keep it reasonable in an approximately 1,000 square foot space?
This is sort of what I'm looking at building. The lean to would be sort of a porch for us facing the rest of our property. This building will be as far to the back corner as I'm legally allowed to build. Planning on a 10' head height with an 8' wide lean to. Trying to get a 4/12 roof pitch.
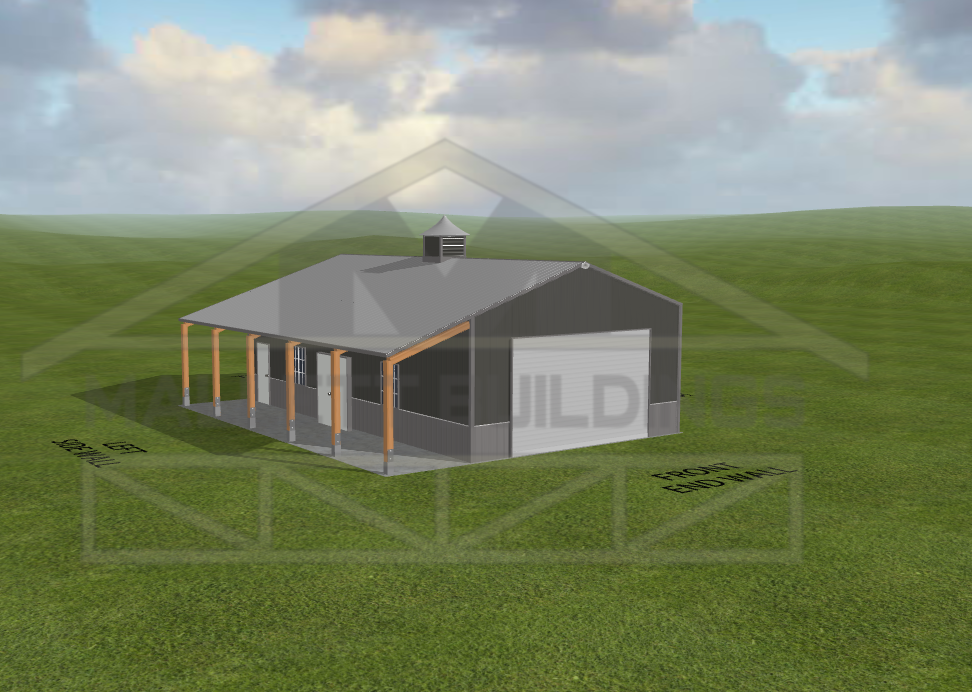
We will be roughing in plumbing; and electrical will be going in as well.
Posted on 9/20/24 at 9:47 am to dewster
where did you find this drawing? This is almost exactly what Im wanting to build
Posted on 9/20/24 at 9:59 am to LCboi
looks like he may have made it himself, the mallet website has a 3D building tool.
Posted on 9/20/24 at 10:33 am to LCboi
quote:
where did you find this drawing? This is almost exactly what Im wanting to build
I used the 3d building tool on the Mallet website. It's a very good for visualizing what you are looking for.
Mueller has a similar tool.
Posted on 9/20/24 at 10:49 am to dewster
Would definitely extend the lean-to out a few feet. 10’ minimum.
Posted on 9/20/24 at 11:39 am to dewster
You may want to consider getting spray foam insulation if yall are going to be in there a lot.
A mr cool mini split would keep it cool. I had an electrician run the power to mine but installed the rest myself. They're precharged so pretty simple to get up and running
A mr cool mini split would keep it cool. I had an electrician run the power to mine but installed the rest myself. They're precharged so pretty simple to get up and running
Posted on 9/20/24 at 4:13 pm to dewster
If you have concerns about the wood rotting on the pole barn(I did) you can build it like a house also. I had mine framed with 2x6s on 16” centers, 11’ walls, 6/12 roof. Cost was between pole barn and red iron of the same size. There’s a few other nice things, the walls are sheathed like a house, you have studs to mount things to, you can use pre sized insulation batts to insulate the walls. Just a suggestion you might not have considered.
Posted on 9/21/24 at 9:35 am to bigbuckdj
Outfit outta nacogdoches texas just finished a friend's shop and did a great job. Looks good. I can see who he used...
I will say this about mallet. Make sure your arse is there when they pour concrete. Pull strings and measure and make sure you get your 4 inches in the middle.
They'll crown the shite out of it either through laziness or to save concrete but 1/2" thick in the middle of your shop where you park all your shite isn't a good place to have the thinnest concrete.
I will say this about mallet. Make sure your arse is there when they pour concrete. Pull strings and measure and make sure you get your 4 inches in the middle.
They'll crown the shite out of it either through laziness or to save concrete but 1/2" thick in the middle of your shop where you park all your shite isn't a good place to have the thinnest concrete.
Posted on 9/21/24 at 1:45 pm to dewster
Insulation Is 100% worth it. I have a Mueller with insulation and 10’ walls. No a/c. My shed only gets as hot as the outside air. And it’s warm in the winter. My neighbors have various brands without insulation and it gets HOT inside. You feel the heat radiating from the roof, and their roofs are a good bit higher than mine.
If I had to build it again, I might build a Mallet. But it would be insulated. It also helps noise a lot in the rain.
If I had to build it again, I might build a Mallet. But it would be insulated. It also helps noise a lot in the rain.
Posted on 9/22/24 at 6:43 am to dewster
Build it as big as you possibly can,you will run out of room fast! I used Mallet 10 years ago,shop is doing fine,even after going through a fire and being rebuilt.I would make the lean too a little wider,minimun 12 foot sides,on shop and have it insulated and sheet the inside walls,if you are installing receptacles,install plenty,or invest in a wall mounted cord reel on each corner,also,outside outlets are a great addition.The Mallet higher grade building are built very well,it will not rot from water intrusion or ground water intrusion,just because of the way they are built.everything that touches the ground is either incased in plastic,or sits on concrete with a metal outside protection barrier.The one thing I wish I had done is built mine 16 feet tall,I went 12 feet ,while it works,I can not park my RV inside the shop.I had to build a seperate RV cover.Get the concrete finisher to put and extra smooth finish on,buy them a case of beer and a pizza,they will hook you up! Air conditioning,I would look at a mini split unit for sure.
This post was edited on 9/22/24 at 6:49 am
Posted on 9/23/24 at 8:53 am to dewster
There is little to no cost benefit to pole barn construction compared to traditional framing. The same is true of steel buildings. The shell may or may not go up slightly faster but interior finishes will take the same amount of time or longer. The building in the drawing built with 4/12 trusses on a slab would probably be slightly less expensive and easier to DIY with traditional framing compared to either steel or pole construction. The added benefit is someone can get a traditional mortgage on it should you decide to sale someday, which may or may not be possible with non-traditional building methods.
Posted on 9/23/24 at 10:36 am to AwgustaDawg
Good stuff! So you’re referring to 2x4 stud walls with trusses along the top on some spacing?
I’m probably not understanding correctly, but it seems like the only difference is you’re using a bunch of 2x4 lumber instead of a small handful of 6x6 or 8x8 posts.
I’m probably not understanding correctly, but it seems like the only difference is you’re using a bunch of 2x4 lumber instead of a small handful of 6x6 or 8x8 posts.
This post was edited on 9/23/24 at 10:58 am
Posted on 9/23/24 at 12:04 pm to turkish
I used 2x6 on mine to get a little more strength and insulation depth but basically yes, instead of having larger posts sitting in the ground you have stud walls anchored to the slab. It also gives you the option of using beams and having a ceiling and attic.
Posted on 9/23/24 at 12:08 pm to turkish
quote:
Good stuff! So you’re referring to 2x4 stud walls with trusses along the top on some spacing?
I’m probably not understanding correctly, but it seems like the only difference is you’re using a bunch of 2x4 lumber instead of a small handful of 6x6 or 8x8 posts.
yes. By the time you add girts and window/door framing the board feet of lumber in a pole type building is about the same as it is in traditional framing with trusses or stick built roof. There are more options with open spaces in pole type construction but trusses will accomplish the same thing in traditional framing.
Building a pole barn without walls is very fast and inexpensive compared to doing the same thing with traditional framing....thats why so many ag buildings are built that way. Its also possible to build a pole building without any kind of foundation other than the posts and finish the foundation at a later date OR make changes in interior walls etcetera. Trusses mitigate the latter.
Pole barn construction for ag type buildings is very fast and easy to DIY. When you are doing one for a house it is about the same as traditional framing. The upside to traditional framing is there are waaaaaayyyyyyy more contractors and skilled labor accustomed to traditional framing.....it can be substantially cheaper because of this. There is also the aversion to alternative framing methods in the banking and insurance industries to contend with AND with local building authorities. Some areas of the country are getting accustomed to pole building but it still lags traditional framinig by a wide margin.
This post was edited on 9/23/24 at 12:14 pm
Posted on 9/23/24 at 12:18 pm to bigbuckdj
quote:
I used 2x6 on mine to get a little more strength and insulation depth but basically yes, instead of having larger posts sitting in the ground you have stud walls anchored to the slab. It also gives you the option of using beams and having a ceiling and attic.
Not to derail but did you do a cost analysis on 2X6 walls over 2X4? I am in the process of designing our retirement home and I am doing everything I can think of to mitigate uncontrolled costs with a fixed income. We have the income to build 2X6 walls now but energy costs in the future may become a problem on a fixed income. From what I have found the energy savings is negligible in the south...it is certainly worth the slight increase in building costs where heating is expensive but everything I have found suggests that the ROI in the south is negligible.
Posted on 9/23/24 at 12:27 pm to turkish
quote:
Good stuff! So you’re referring to 2x4 stud walls with trusses along the top on some spacing?
I’m probably not understanding correctly, but it seems like the only difference is you’re using a bunch of 2x4 lumber instead of a small handful of 6x6 or 8x8 posts.
One other caveat. You may be in an area of the country where your local building authority has some common sense. They are few and far between but they do still exist. IF you do indeed live in such an area and can use sawmill lumber to build a pole type structure you can do it for much less than you can using kiln dried and grade stamped lumber. The same holds true for traditional framing BUT traditional framing methods are not as forgiving when green lumber is used as pole framing is. Once a pole structure is tied together lumber tension (twisting, warping and cupping) is very kind.....hundreds of thousands of barns still being used which were built with lumber which was milled and nailed together without any issues. Lumber so green you had to chase the squirrels out of it. That method is still viable UNLESS you live in an area where big lumber has convinced elected officials you are too stupid to do what people have done for thousands of years all over the world. Unfortunately that applies to probably 95% of the United States.
Kiln dried grade stamped lumber is only "better" when it is grade stamped and removed from the kiln, in the moment. After that it does exactly what all lumber does.....it reaches what passes for equilibrium in moisture content compared to the environment it is in. What it does do for a certainty is eliminate competition from small sawyers and makes it possible to ship lumber from the PNW to the SE without it twisting, warping and cupping to the point of uselessness....it will do it once it hits the lumber yard but it will be pretty as hell for a few weeks.
Posted on 9/23/24 at 12:29 pm to AwgustaDawg
I did not do any kind of analysis but my shop is 26x32 enclosed, it was a small cost to use 2x6 for me. I could certainly see it not paying back on energy alone if you consider the additional lumber and insulation costs. The money might be better spent on nicer windows or a more efficient AC for energy savings in your scenario
Posted on 9/23/24 at 1:52 pm to AwgustaDawg
Glad to see someone taking that stance. Rough cut lumber can be great stuff.
Posted on 9/23/24 at 2:10 pm to AwgustaDawg
Interesting. Is green lumber that much cheaper? I had it in my head that having a portable sawmill on site was not a huge savings over store bought.
Popular
Back to top
